1.0 Introduction Process Control System
A process control system is made up of a group of electronic devices that provide stability, accuracy and eliminate harmful transition statuses in production processes. Operating systems can have different arrangements and implementation, from energy supply units to machines. As technology quickly progresses, many complex operational tasks have been solved by connecting programmable logic controllers and a central computer. Beside connections with devices (e.g., operating panels, motors, sensors, switches, valves, etc.) possibilities for communication among instruments are so great that they allow a high level of exploitation and process coordination. In addition, there is greater flexibility in realizing a process control system. Each component of a process control system plays an important role, regardless of its size. For example, without a sensor, the PLC wouldn't know what is going on during a process. In an automated system, a PLC controller is usually the central part of a process control system. With the execution of a program stored in program memory, PLC continuously monitors status of the system through signals from input devices. Based on the logic implemented in the program, PLC determines which actions need to be executed with output instruments. To run more complex processes it is possible to connect more PLC controllers to a central computer. A system could look like the one pictured below:
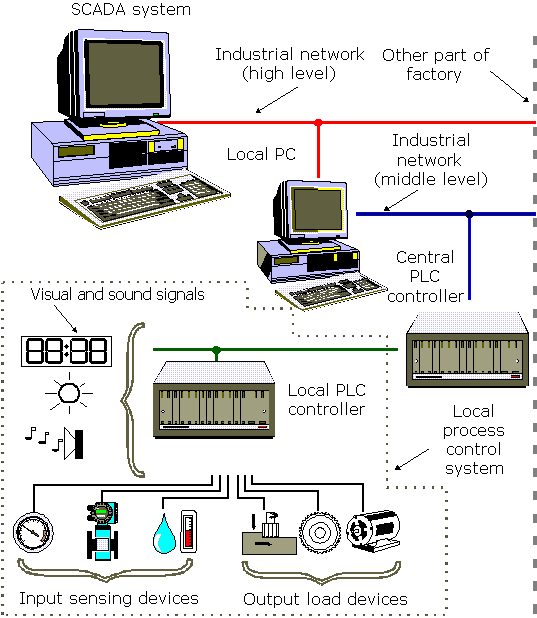